As an engineering manager, I commonly have questions regarding heavy duty work lights from cost to quality. With my experience, I understand that temporary lighting specifically heavy duty lighting is built to the most exact standards for areas where classified location lighting is required.
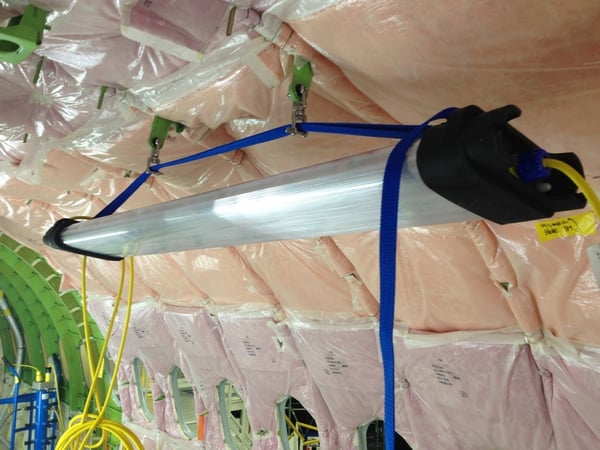
1. You can get by with low cost “disposable” units for this job only.
While you certainly can buy an inexpensive unit, you will likely get what you pay for. Low cost imported units are notorious for lack of durability on the jobsite. So if you need 50 for this job, you had better factor in the cost of buying 70 to have enough to finish the job. Unfortunately, you might not find that out until part of your crew is already in the dark.
2. Temporary heavy duty lighting is too expensive.
You can still find quality American made heavy duty lighting, and believe it or not, they can be purchased for a reasonable price. You might not be able to get one as cheaply as the cheapest import model you can find, but if you factor in the fact that you can re-use a quality unit for two or more jobs, you have already cut the effective cost in half. You can hedge your bet by ordering RFID equipped items for ease of inventory tracking and theft prevention. That will help make sure you do in fact get several (or more) uses out of your investment.
3. Heavy duty lighting is big & heavy.
Heavy duty industrial portable lighting has gone through a revolution in the last few years as LED technology has become mainstream. The old, large incandescent and fluorescent fixtures have been replaced with smaller and lighter LED based fixtures. These smaller lighting fixtures put out abundant white light in a smaller, lower-powered footprint.
4. Heavy duty lights get too hot!
As the power required to make the light has decreased with the advent of mainstream LED technology, so has the heat associated with the lamp. No more burning your knuckles on a hot lamp guard.
5. Heavy duty lighting has a long lead time.
If you buy from the right vendor, you can deal with an American manufacturer who has stock on the shelf or can assemble your order from standard components kept on the shelf. Either way, it is not necessary to speak another language or have to wait 10 weeks for overseas delivery.
6. Heavy duty lighting is not customizable (and in small quantities).
If you buy from the right vendor, you can in fact have your order customized, even if it is only for a few units. You can request longer or shorter cords, extra receptacles, custom cord labeling or custom product labels, or even the addition of RFID tags for theft prevention.
Tag(s):
Jobsite Lighting
Jeff Angle
Jeff is the Chief engineer, PE & Six Sigma Blackbelt with 25 years in the biz. His degree is in Electrical Engineering from University of Akron and has an extensive background in product development, UL regulatory compliance & ISO9001 quality assurance.
More from the blog
View All Posts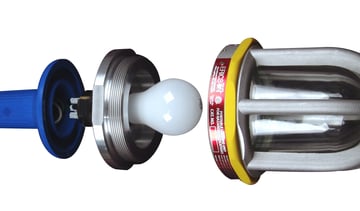
Workplace Safety
2 min read
| March 16, 2020
What is explosion proof or hazardous location lighting?
Read More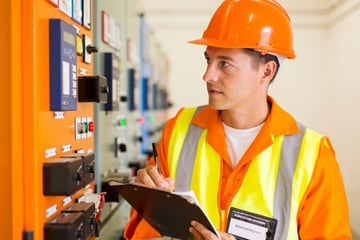
Workplace Safety
2 min read
| August 30, 2016
Why Your Electrical Safety Provider Should Have Engineering Expertise
Read More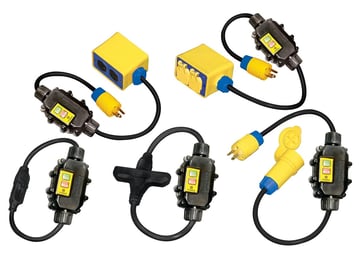
Wiring Devices
3 min read
| March 23, 2021
NEC Code Changes and Worker Safety
Read MoreSubscribe to blog updates
Stay up-to-date on what's happening at this blog and get additional content about the benefits of subscribing.