Shedding a Light on Safe and Compliant Jobsite Lighting
Proper light levels on construction sites are critical to worker productivity and jobsite safety. Safe light levels are outlined in OSHA Standard 1926.56 where safe minimum light levels for various areas of operation within a jobsite. Below is a brief extract from OSHA Standard 1926.56(a) -
Foot-Candle Levels | Area of Operation* |
5 |
General Construction Area Lighting |
3 |
General Construction Areas, concrete placement, excavation and waste areas, access ways, active storage areas, loading platforms, refueling, and field maintenance areas |
5 |
Indoors: warehouses, corridors, hallways and exit ways |
5 |
Tunnels, shafts, and general underground work areas: (Exception: minimum of 10fc is required at tuna and shaft heading during drilling, mucking and scaling. Bureau of Mines approved cap lights shall be acceptable for use in the tunnel heading) |
10 |
General construction plant and shops (e.g., batch plants, screening plants, mechanical and electrical equipment rooms, carpenter shops, rigging lofts and active store rooms, mess halls and indoor toilets and workrooms.) |
30 |
First aid stations, infirmaries, and offices. |
Now that we know the minimum light levels how do we design our work sites to meet those minimums in hazardous area?
First, we need to know about the space or atmosphere from a hazardous location perspective, we are lighting. Through rigorous testing, UL has developed environmental classifications around hazardous atmospheres these spaces might contain. Understanding these atmospheres is critical to hazardous lighting fixture selection and wiring methods necessary to power these fixtures.
Per Article 500 of the National Electrical Code (NEC), an area is considered a hazardous location when there are (or may be) ignitable concentrations of combustible substances in the air. These substances include vapors, dust, certain fibers, and flammable gasses. Through rigorous testing UL has separated the atmospheres (spaces) in to three distinct categories which list the primary hazardous material in each space –
- Gases, Vapors or Liquids
- Dust
- Fibers and Flyings
Next there are Groups, (A-G) which list the specific hazardous material present in a space and then Divisions (1 or 2) which list the conditions in which these hazardous materials existing in the atmosphere – essentially Normally present, Suspended or Used or Not Normally present, Suspended or Stored.
Below is a summary of Classes I, II and III Hazardous locations.
Explosion proof lighting is a special type of product designed to withstand the toughest environments, specifically hazardous locations. To be considered explosion proof, a lighting fixture must be able to contain an internal combustion by preventing it from propagating outside the unit.
Many people assume that these fixtures work via a seal around the bulb (and its other components), which prevents flammable compounds from entering the device. However, that's only half the story. Explosion proof lighting contains a unique feature called a flame path, which is a special type of joint between different parts of the enclosure. This flame path is essentially a controlled leak that allows expanding gasses from an internal explosion to cool and safely vent to the outside, without igniting any explosive atmosphere that may be outside the lamp. The class, division and group that the enclosure is rated for determines the allowable leak rate (flame path gap and length) to prevent external ignition. For example, a Group A enclosure for acetylene has a much smaller leak rate than a Group D enclosure for propane.
It is worth noting that products that are appropriate in hazardous areas are not always explosion proof. There are many other methods to mitigate explosion risk. Other techniques include intrinsic safety, encapsulation, oil immersion, pressurization, and so on, depending on each application’s specific needs. Project managers should review a product's certifications prior to bringing it to the job site to ensure the equipment is appropriate for their specific application
Now that we’ve determined the minimum amount of lighting for a given space and that spaces atmospheric condition, here is where the science of lighting is applied. The IES (Illuminating Engineering Society) has recommendations for several workspaces and has developed requirements and standards on which fixture manufacturers test their fixtures and publish their fixtures data. Lighting designers use this data with lighting software to design a particular space, considering the size the area to be illuminated, mounting height, surface reflectance and minimum light levels. These figures combined with fixture performance will give the number of selected fixtures and spacing to achieve the desired light level in the selected area.
Understanding the atmosphere of the space to be lit, the minimum lighting levels for safe and efficient working conditions is essential to selecting and designing and applying lighting to achieve a safe and productive workspace.
*Ref: OSHA Regulations, 1926.56 - Illumination
Brian Earl
Hailing from Minnesota originally, Brian began his secondary education at the University of Minnesota with his undergraduate work and his MBA in Management at University of Michigan, focusing on strategic marketing and market planning. He has an extensive background in developing and leading a variety of marketing,...
More from the blog
View All Posts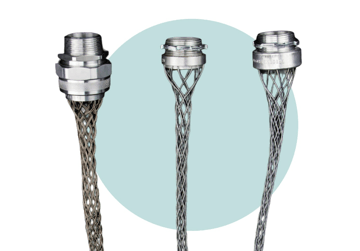
Strain Relief and Cord Grips
7 min read
| March 14, 2024
The Importance of Wire Mesh Strain Relief for Portable Cords
Read More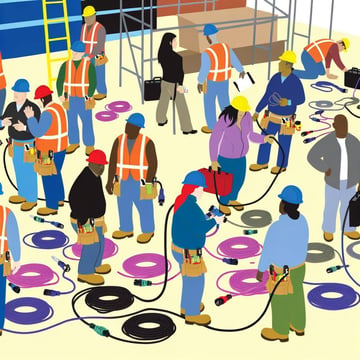
Workplace Safety
2 min read
| June 12, 2024
Protecting Workers and Cords From Harm, Safety Through Compliance
Read More
Certifications and Regulations
4 min read
| March 12, 2024
Why Contractors Should Use Certified ETL Portable Power
Read MoreSubscribe to blog updates
Stay up-to-date on what's happening at this blog and get additional content about the benefits of subscribing.